期間工や派遣工でライン作業で働いている方、作業に間に合っていますか?
決められた時間内に決められた仕事を淡々とこなす。
口で言うのは簡単ですけど、実際にやってみると大変ですよね。
今回はトヨタグループの組立ラインで10年以上ライン作業をしている私が、ライン作業が間に合わない人に向けて、ライン作業を間に合わせるためのヒントをお伝えします。
職場先輩や上司によっては…。
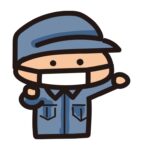
もっとがんばれっ!
早く!早く!
コツやポイントも教えずに、根性論や雰囲気だけのアドバイスしかしない、できない人もいます。
職場先輩や上司に期待できないんなら自分で何とかするしか有りません。
大丈夫です。ラインに間に合っている人も、間に合わない人も大きな差は有りません。
少しのコツを知るだけで、簡単に間に合うようになることも多いです。
一緒に上手になるコツを知って、ラインに間に合うようにしていきましょう。
自分がライン作業に向いているか不安な方は、こちらの記事もご覧ください。
5つの質問に答えるだけで、ライン作業に向いているかわかります。
ライン作業が間に合わない理由|“きつさ”の正体とは?
「なんでこんなに間に合わないの?」と焦る人は多いです。
でも、実は原因にはいくつかパターンがあります。
まずは“自分の何が詰まっているのか”を知ることが改善の第一歩です。
作業に慣れていない
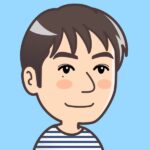
作業に慣れていますか?
まず最初はここからです。
作業への慣れが足りなければ、間に合わないのも当然です。
作業に慣れているか?作業への理解は十分か?を自分で確認してみましょう。
自動車工場のライン作業は、担当する仕事も多く、覚えることもたくさん有ります。
作業を始めて間もない時は、間に合わせる事よりも、作業に慣れる事を優先しましょう。
頭で考えずに体が動くようになっていれば、作業への慣れは十分です。
まずは担当する作業に慣れて、滞りなくスムーズに体が動くような状態を目指しましょう。
無駄な動きが多い
ライン作業が間に合わない人は、無駄な動きが多い傾向が有ります。
無駄と言っても、見るからに余計な動きをしているだけでなく、小さな無駄の積み重ねでラインに間に合わない人は多いです。
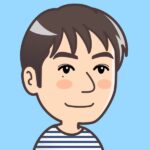
他の人より1歩歩行が多い。
他の人が両手で1回で取り出す部品を片手で2回かけて取り出す。
他の人より確認回数が多い。
振り向きがやたら大きい。
等、1回1回の無駄な時間は少ないですが、数回無駄を重ねるとかなりのタイムロスになります。
1サイクルの作業で3秒ロスすると、10サイクル作業すると30秒です。
1サイクル60秒ですと、もう半分遅れています。
これでは作業に間に合いません。
「塵も積もればなんとやら」と同じで、「無駄も積もれば間に合わない」です。
焦ってしまう

ライン作業に間に合わないから、急いで作業をして、焦ってミスをしてしまう。
焦ってミスをして作業に遅れるから、さらに焦ってミスを繰り返してしまう。
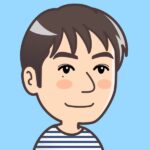
卵が先か鶏が先か?
焦りやすい人はこの負の連鎖にはまっていきます。
焦って作業してもいい事は有りません。
作業ミスのタイムロスは大きいです。作業ミスを減らすことがライン作業に間に合わせる1番のポイントかもしれません。
責任感(プライド?)が強い
責任感(プライド?)が強くてラインに間に合わない人もいます。
完全に作業が出来て、ラインに間に合うベテランになって責任感が強いのならまだいいのですが、作業が間に合わない状態での責任感は邪魔です。
作業が遅れても、責任感(プライド?)が邪魔して職制を呼べない人もいます。
作業をミスしても、責任感(プライド?)が邪魔をして自分で何とかしようとする人もいます。
イレギュラーに対応するためにライン進行である職制がいるのに、呼び出すことをためらう責任感(プライド?)が強い人もラインに間に合わない傾向が有ります。
体力不足
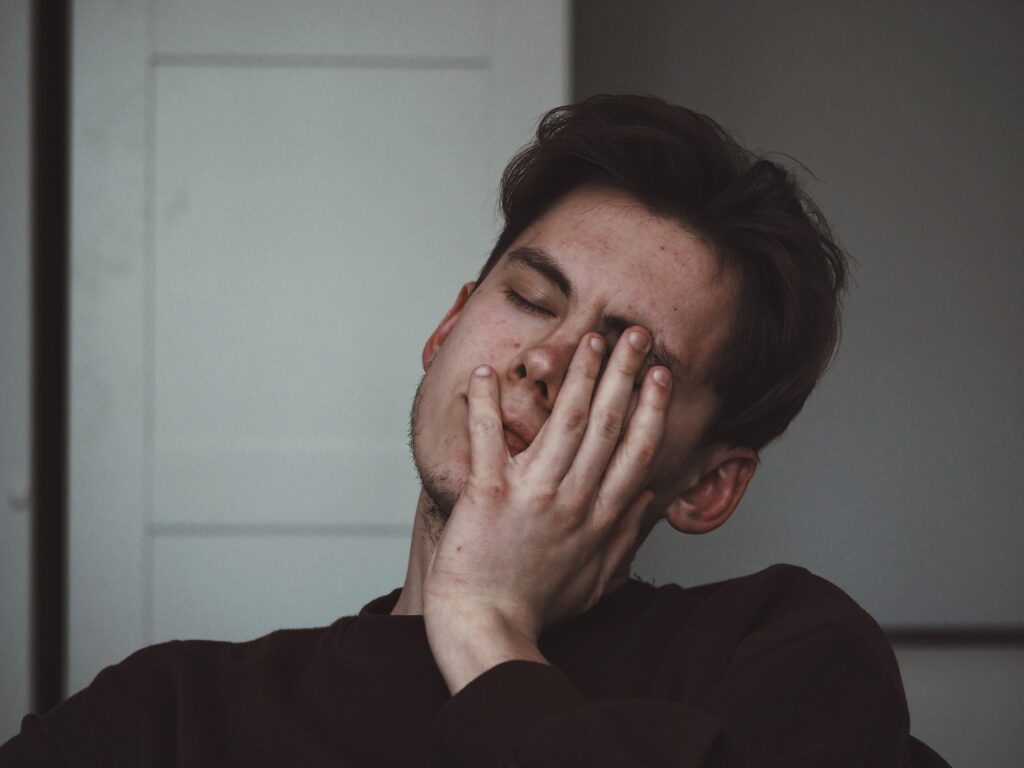
根本的に体力が不足してラインに間に合わない人もいます。
自動車工場の組立ラインは、正直ハードです。
1日中ずっと動き続けます。
自分が疲れても、ラインスピードは一定のまま流れ続けます。
残業時間になるとみんな疲れが顔に出ます。
残業時間になるとラインに間に合わなくなる人は、体力不足かもしれません。
そもそも間に合わない行程
これは完全なハズレ。イレギュラーです。
そもそも間に合わない設定の工程が存在します。
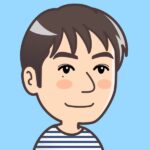
…無理ゲーじゃん。
そうなんです。無理ゲーなんです。
オプション作業や生産比率によって、現れてしまう「そもそも間に合わない行程」
ここが自分の持ち場だと正直しんどいです。
行程ガチャでハズレです。
反対直の人や、職制が入っても間に合わない行程だったらハズレ工程ほぼ確定です。
自分の工程にハズレを感じたら下の記事を読んでみて下さい。
ハズレ工程のチェック方法がわかります。
ライン作業が苦痛でしかない
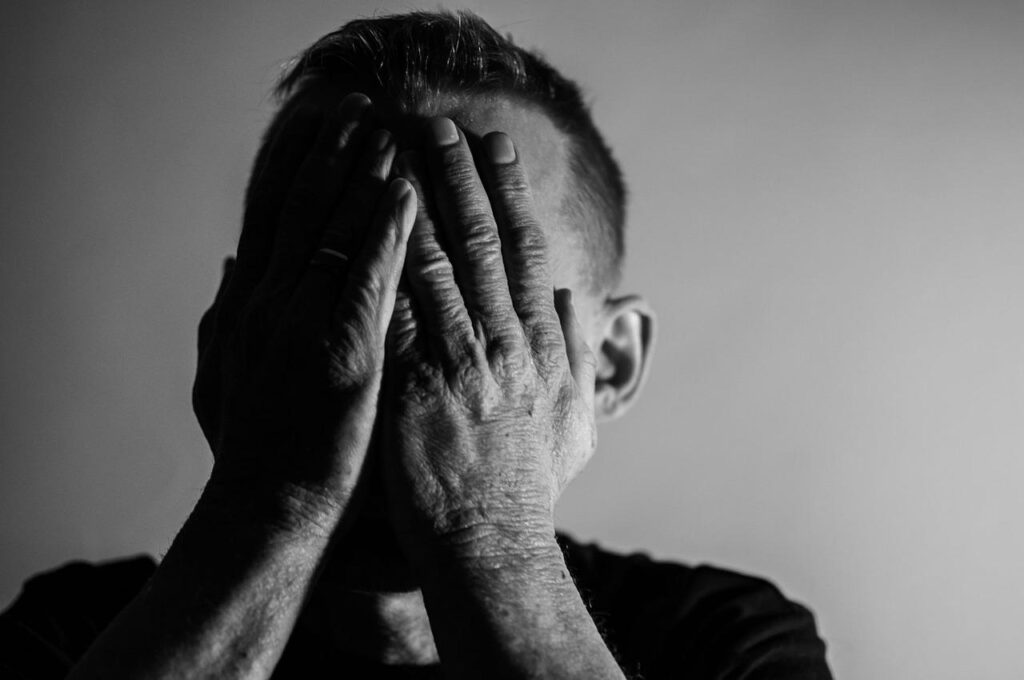
最後は「ライン作業が苦痛でしかない」です。
人には向き、不向きが有ります。
自分で、
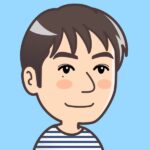
向いていないな。
辛いな。
辞めたいな。
と頻繁に思うようになったら、もう無理です。
気持ちが折れているので、ラインに間に合わせることは出来ません。
と言うか「ラインに間に合わせよう」というモチベーションにもならないでしょう。
無理して頑張るよりも、転職を考えた方が良いかもしれません。
無理して仕事をするストレスは相当なものです。
「‥でも、いままで工場関係でしか働いたことがないから、他の業種に行くのは不安。」
そんな人も安心な製造業から他業種の転職に特化したサービスもあります。
自分に製造業が向いていないと思ったら、一度相談してみるのはいかがですか?
製造業出身のエージェントがあなたの転職をサポートしてくれます。

ライン作業がきつい時に乗り越える7つの対処法
間に合わないと感じる原因が分かれば、あとは行動あるのみ。
ここでは、私自身や周りの経験から“本当に効果があった”と感じた7つのコツを紹介します。
まずは作業に慣れる
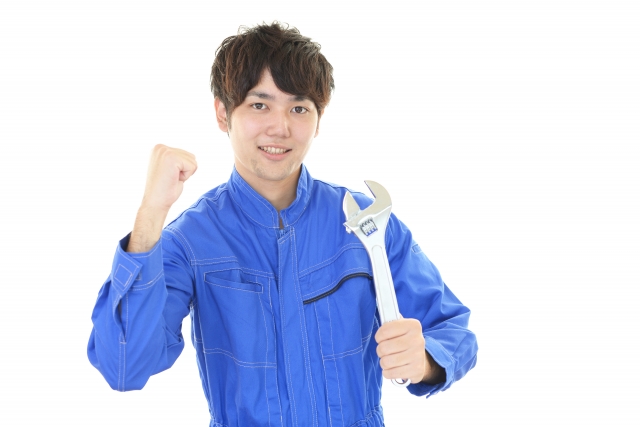
仕事の種類にもよりますが、自動車工場の組立ラインの作業ですと、覚えることも多く、1日、2日ではなかなか仕事に慣れません。
トヨタ自動車では、配属から1か月程度で独り立ち出来れば普通です。
焦らなくて大丈夫です。
仕事によって、おおよその1人立ちまでの期間が決まっているので、期間内に仕事に慣れるようにしましょう。
わからない事、疑問に思ったことは、どんどん質問していきましょう。
頭で理解して、体に覚えさせる。この流れがいいでしょう。
1人立ちまでの期間をいっぱいに使って、作業に慣れましょう。
「…あれっ、そろそろ間に合わないとヤバない?」
こんな風に思った人は下の記事もご覧ください。
どれくらいで一人立ちすれば、目を付けられないのかボーダーラインがわかります。
身体のメンテナンスは忘れずに
疲れがたまっていたり、身体を痛めたりしていたら、ライン作業に間に合わないのも当然です。
特に働き始めの頃は、無理をして体を痛めやすいので、日々のメンテナンスは欠かせません。
ライン作業前の体操、パラフィン浴、ストレッチ、帰宅後に趣味に没頭するなどして、心身ともにメンテナンスをしっかりと行いましょう。
自動車メーカーのライン作業では、体感だと初心者の9割は指が痛くなります。
指が痛くなると、ラインに間に合わせるなんて不可能です。
それどころか、痛い指で無理してか頑張りすぎると、日常生活にも支障をきたす【ばね指】になります。
1日中インパクトレンチを使うライン作業をしている人は要注意です。
詳しくは下の記事をご覧ください。
ばね指の原因と予防法がわかります。
指以外にも1日中動き続けるライン作業では、体の負担は大きいです。
ライン作業で痛めやすい体の部位をパパっと知りたい方は下の記事もご覧ください。
痛めやすい部位を知っているのと、知らないのとでは身体への労わり方が違います。
自分の作業を見直してみる
無駄な動きが無いか?
改善できる点は無いか?
自分の作業を見直してみましょう。
おススメの方法は3つ。
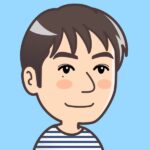
職制にアドバイスをもらう。
自分の作業の動画を撮ってもらう。
反対番の作業を参考にする。
自分で考えてもなかなか、無駄も改善点も見つかりにくいです。
そんな時は、職制にアドバイスをもらいましょう。
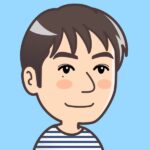
この作業、合わせ位置が見えにくくてセットするのに時間がかかってしまいます。位置合わせのポイントとか有りますか?
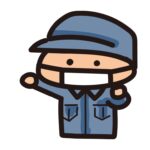
この位置からだと合わせ位置が見やすいから、この位置に立ってセットしてみて!
こんな風にピンポイントで聞くと、アドバイスもピンポイントなものをもらいやすいです。
もう1つは、自分の作業を動画で撮ってもらうことです。
撮ってもらった動画を後で観てみると、無駄な所、改善点が見えてきます。
工場によっては撮影禁止の所も有るので、動画撮影は職制の許可をもらいましょう。
自分では、無駄がない動きだと思っていても、意外と動画で観てみると直せそうなところが沢山出てきますよ。
後は反対番の作業を参考にするのも、おススメです。
同じ作業をしている人ですからね。
反対番がラインに間に合っているのであれば、その動きを真似すれば100%ラインに間に合います。
ライン作業に間に合っていないのであれば、参考にしないのは勿体ないです。
平常心を心がける
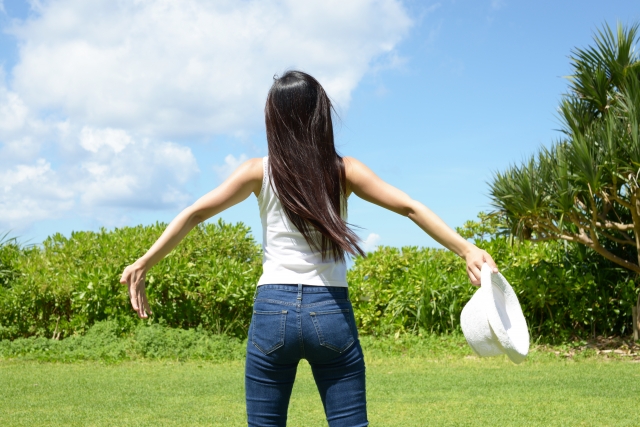
ライン作業を間に合わせるためには、平常心も大事です。
慌てたり、焦ったりすると、どうしてもミスが増えます。
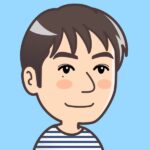
遅れないように速くやらなきゃ!
この考え方の時点で、すでに平常心ではありません。
- 丁寧に作業する。
- 急がずに淡々と同じリズムで作業する。
この2つを意識して作業するようにしましょう。
1人で頑張り過ぎない
作業が遅れた時や、ミスをしたときは迷わず職制を呼びましょう。
自分で遅れを挽回したり、ミスを修正したりしようとしてもほとんどの場合うまくいきません。
急いで、焦って、ミスをして、負の連鎖にはまります。
遅れをひどくするだけならまだしも、不具合やキズを発生させることにもなるので、何かあった時は迷わず職制を呼び出しましょう。
「いつもと違ったら全て異常」です。
1人で製品を造っているわけではありません。
みんなで製品を造っているのです。
異常を対処するのが職制の仕事ですので、何かあったらすぐに連絡しましょう。
体力が続くようにペース配分する
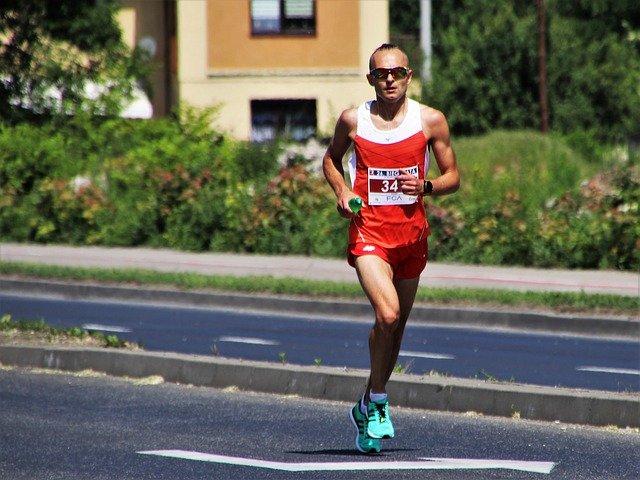
体力が続かなくてライン作業に間に合わない人は、体力が足りないのではなくてペース配分が出来ていないことも多いです。
ライン作業は、ずっと動きっぱなしなのでどうしても疲れて、遅れてしまうことが有ります。
間に合わせるために一生懸命動いて、残業時間になると体力がなくなってしまう。
こんな人は、始業から出来るだけ、一定のペースで作業を行うようにしましょう。
ペースのバラツキは、思いのほか体力を奪います。
体力温存には、始業から出来るだけ一定のペースでエコモードで作業しましょう。
諦めも肝心
そもそも間に合わない行程を担当したら、もう潔く諦めましょう。
職制も、同僚も間に合わない行程なのはわかっています。
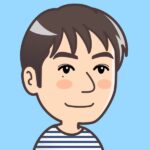
この比率だと遅れるな。
このオプション来たら無理だな。
こう思ったら、早め早めに職制を呼び出しましょう。
だって自分の頑張りだけでは無理なんですもの。
諦めも肝心です。
ライン作業に間に合わなくても1か月は頑張りませんか?
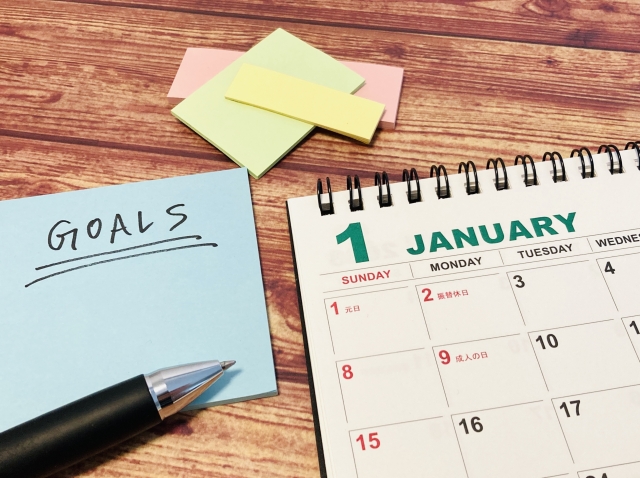
担当するライン作業に間に合っていない人も、とりあえず1か月頑張ってみることをおススメします。
最初は、絶対に間に合わないと思っている仕事が、気づけば間に合うようになっているのは、ライン作業あるあるです。
自分がライン作業に間に合わない要因を知って、上手になるコツを実践して1か月頑張ってみましょう。
色々考えるのはそれからです。
1か月後に全くラインに間に合っていなくて、心身ともにつらい時になったら、そこで転職を考えましょう。
他の工程、他の工場に移動すれば簡単に間に合うようになるのは、工場あるあるです。
「もう無理!」と思ったら、さっさと転職してしまうのが幸せになる近道です。
別に今の工程が間に合わないからといって、工場のライン作業を全部苦手と思う必要は全くありません。
高収入で好待遇で働ける工場勤務を全て諦めるなんて、もったいないですよ。
とりあえず、他の工場で再チャレンジしてみることをおススメします。
工場の仕事は配属先によって当たりハズレが大きいですからね。
「いざとなったら転職する!」こう思うだけでも精神的に楽になりますよ。
気になる方は、工場求人をたくさん扱っているところに相談してみるのもアリです。
同じメーカー、同じ工場でも、担当する仕事によって天国と地獄に分かれる可能性のある期間工のお仕事。
今の所が無理だからといって、期間工自体が無理なわけではありません。
見切りをつけたら、密かに転職活動しておくこともおすすめです。
ライン作業がつらくても大丈夫|焦らず自分のペースを見つけよう
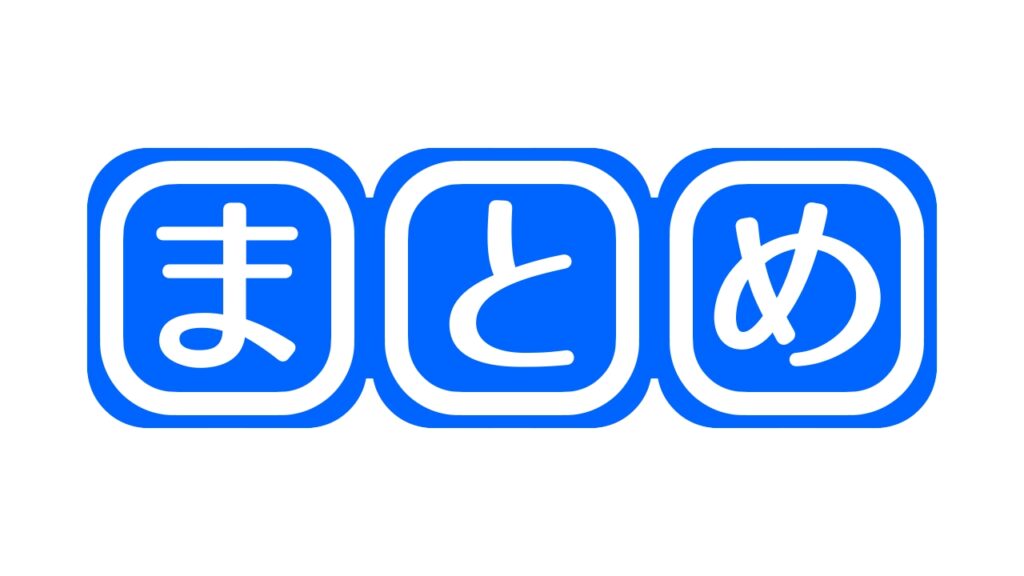
今回はライン作業が間に合わない人に向けて、間に合わない7つの要因と、上手になる7つのコツを解説しました。
以下にまとめておきます。
ライン作業に間に合わない7つの要因
- 作業に慣れていない
- 無駄な動きが多い
- 焦ってしまう
- 責任感(プライド?)が強い
- 体力不足
- そもそも間に合わない行程
- ライン作業が苦痛でしかない
ライン作業が上手になる7つのコツ
- まずは作業に慣れる
- 身体のメンテナンスは忘れずに
- 自分の作業を見直してみる
- 平常心を心がける
- 1人で頑張り過ぎない
- 体力が続くようにペース配分する
- 諦める
ライン作業に間に合わないと体力だけでなく、精神的にも疲弊していきます。
まずは間に合わない要因を知って、上手になるコツを試してみませんか?
少しのコツを掴むだけで、淡々と一定のペースで作業できるようになり、ラインに間に合うようになります。
1回コツを掴めば、他の作業にも応用が利くので、もっと給料のいい会社でライン作業をすることも可能です。
ライン作業に乗れるようになって、精神的に余裕が出てきたら他の会社の条件も比べてみましょう。
もっと効率的に稼げるメーカーが有るかもしれませんよ。
配属先や担当する仕事に差はあっても、基本的に期間工のお仕事はどこのメーカーも同じ感じ。
だったら、給料や待遇ができるだけいいところで働きたくはありませんか?
期間工案件をたくさん持っている、派遣会社なら色々なメーカーを比べて選べます。
詳しくは↓をチェック!
ライン作業に間に合わなくて悩んでいる人の参考になれば嬉しいです。
最後まで読んでいただき、ありがとうございました。
コメント